فرایند مهندسی پوسته های بتن GFRC و UHPC
در رویداد FacadeForum 2019، من افتخار داشتم که در ارائهای از آقای رضا صالحی از بخش تحقیق و توسعه در مشاور نمای آلومگلس حضور داشته باشم. صحبت او بر چالشهای مهندسی متمرکز بود که در طول تولید پنلهای بتن مسلح شیشهای (GRC) برای یک پروژه بزرگ با آن مواجه شدند. به عنوان کسی که به حوزه مهندسی نما علاقه زیادی دارد، بینشهای او را بسیار ارزشمند یافتم و مایلم نکات کلیدی خود را از این رویداد به اشتراک بگذارم.
طراحی پنلهای GRC:
یکی از مهمترین چالشها در این پروژه، طراحی پنلهای GRC بود. معمار طرحی منحصر به فرد و موجدار را برای نما پیشنهاد کرده بود که نیازمند تولید پنلهایی با عمق و ابعاد متفاوت بود. برای مقابله با این چالش، تیم مشاوره نمای آلومگلس یک الگوریتم توسعه داد که فاصله بین پنجرهها و اختلاف ارتفاع را تجزیه و تحلیل میکرد تا یک فریم استاندارد ایجاد کند که بتوان در تمام پنلها از آن استفاده کرد.
بررسی راهکارهای نصب پنل GFRC:
تیم گزینههای مختلفی را برای نصب پنلهای GRC بررسی کرد، از جمله پیکربندیهای عمودی و افقی، و همچنین استفاده از سیستمهای واحد پنل بزرگ. آنها همچنین ادغام تجهیزات و مواد داخلی در این سیستمها را در نظر گرفتند. در نهایت، تصمیم گرفته شد که با ترکیبی از پنلهای افقی و عمودی پیش بروند، که امکان ایجاد یک شبکه منظمتر و تکرارپذیرتر را فراهم میکرد و در عین حال تعداد پنلهای مورد نیاز را به حداقل میرساند.
مهندسی بهینه پنل بتنی:
پس از بررسی دقیق و آزمایش، تیم به یک ماژول پنل نهایی رسید که شامل پنج نوع پنل اصلی (A، B، C، D و E) بود. این ماژول خطاهای احتمالی در تولید را در نظر گرفت و اطمینان حاصل کرد که پنلها تا حد زیادی شبیه طرح معماری خواهند بود. پنل مرکزی و چهار پنل اطراف آن با هم نصب شدند، با یک تلورانس 2 سانتیمتری برای جبران هرگونه تفاوت.
اتصال پنلهای GRC:
جنبه بحرانی دیگر پروژه، اتصال پنلهای GRC به لنگرهای فلکس پشت آنها بود. تیم سیستمی را ابداع کرد که از یک پیچ اصلی برای تنظیم ارتفاع و یک صفحه اتصال با یک پیچ برای تنظیم جانبی استفاده میکرد. این راه حل نوآورانه امکان همترازی دقیق پنلها را در حین نصب فراهم میکرد.
تولید قالب و کنترل کیفیت بتن نما:
برای تولید پنلهای GRC، تیم از یک تکنیک جدید با استفاده از فرمهای پلیاستایرن برش خورده با سیستم برش سیم استفاده کرد. این فرمها بر اساس طرح مهندسی و مدل توسعه یافته برای پنلها بودند. سپس قالبها با استفاده از FRP (پلاستیک تقویت شده با الیاف) تولید شدند. در سراسر فرآیند تولید، اقدامات کنترل کیفیت سختگیرانهای با پیروی از استانداردها و مقررات PCI اجرا شد.
حمل و نقل و نصب پنلهای بتنی نما:
انتقال پنلهای GRC از محل تولید در تهران به محل پروژه در کربلا، چالشهای خاص خود را داشت. برای به حداقل رساندن تأثیر نیروها در حین حمل و نقل، تیم سیستمی را برای جمعآوری و اتصال ایمن پنلها توسعه داد. واحدهای کنترل نیز برای نظارت بر پنلها در طول سفر منتقل شدند. پس از رسیدن به محل، پنلها با دقت و با استفاده از سیستم اتصال طراحی شده نصب شدند.
نتیجه گیری:
ارائه آقای رضا صالحی در FacadeForum 2019 نگاهی جذاب به پیچیدگیهای تولید پنلهای GRC برای یک پروژه بزرگ ارائه داد. تیم مهندسی آلومینیوم شیشه تهران مهارتهای حل مسئله و تفکر نوآورانه استثنایی را در غلبه بر چالشهای مختلف مهندسی که با آن مواجه شدند را در اختیار پیمانکار تولید و نصب این پروژه شرکت سایتال ساخت قرار داد. تجربه آنها به عنوان یک مطالعه موردی ارزشمند برای متخصصان در صنعت مهندسی نما عمل میکند و اهمیت همکاری، انطباقپذیری و توجه به جزئیات را در ارائه پروژههای موفق برجسته میکند.
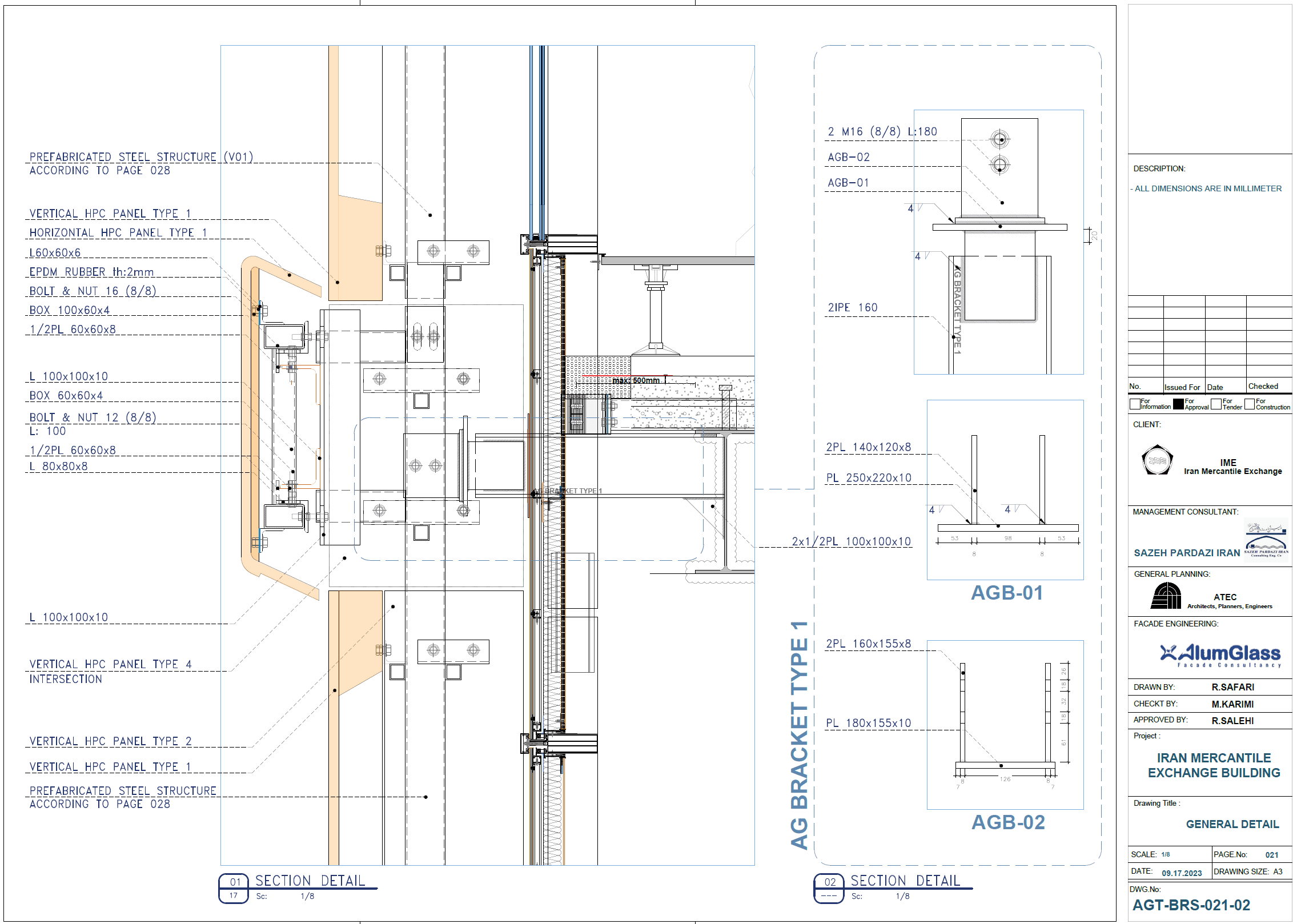
Overcoming Engineering Challenges in GRC Panel Production
Introduction:
At the recent FacadeForum 2019 event, I had the pleasure of attending a presentation by Mr. Reza Salehi from the R&D department at AlumGlass Facade Consultancy. His talk focused on the engineering challenges faced during the production of glass-reinforced concrete (GRC) panels for a large-scale project. As someone deeply interested in the field of facade engineering, I found his insights invaluable and would like to share my key takeaways from the event.
Designing the GRC Panels:
One of the most significant challenges in this project was the design of the GRC panels. The architect had proposed a unique, undulating facade design that required the production of panels with varying depths and dimensions. To tackle this challenge, the team at AlumGlass Facade Consultancy developed an algorithm that analyzed the distances between windows and the height differences to create a standardized frame that could be used across all panels.
Exploring Panel Installation Options:
The team explored various options for installing the GRC panels, including vertical and horizontal configurations, as well as the use of large panel unit systems. They also considered the integration of internal equipment and materials within these systems. Ultimately, the decision was made to proceed with a combination of horizontal and vertical panels, which allowed for a more organized and repetitive network while minimizing the number of panels required.
Developing the Final Panel Module:
After careful consideration and testing, the team arrived at a final panel module that consisted of five main panel types (A, B, C, D, and E). This module took into account potential errors in production and ensured that the panels would closely resemble the architectural design. The central panel and four surrounding panels were installed together, with a 2-centimeter tolerance to accommodate any discrepancies.
Connecting the GRC Panels:
Another critical aspect of the project was the connection of the GRC panels to the flex anchors behind them. The team devised a system that utilized a main bolt for height adjustment and a connection plate with a bolt for lateral adjustment. This innovative solution allowed for precise alignment of the panels during installation.
Mold Production and Quality Control:
To produce the GRC panels, the team employed a novel technique using polystyrene forms cut with a wire cut system. These forms were based on the engineering plan and model developed for the panels. The molds were then produced using FRP (fiber-reinforced plastic). Throughout the production process, strict quality control measures were implemented, adhering to PCI standards and regulations.
Panel Transportation and Installation:
Transporting the GRC panels from the production site in Tehran to the project site in Karbala presented its own set of challenges. To minimize the impact of forces during transportation, the team developed a system to securely collect and connect the panels. Control units were also transferred to monitor the panels during the journey. Once on-site, the panels were carefully installed using the designed connection system.
Conclusion:
Mr. Reza Salehi’s presentation at the FacadeForum 2019 provided a fascinating glimpse into the complexities of producing GRC panels for a large-scale project. The team at AlumGlass Facade Consultancy demonstrated exceptional problem-solving skills and innovative thinking in overcoming the various engineering challenges they faced. Their experience serves as a valuable case study for professionals in the facade engineering industry, highlighting the importance of collaboration, adaptability, and attention to detail in delivering successful projects.